Smart Hybrid Machine Tool and Manufacturing
The current concept of a Smart Hybrid Machine Tool (SHMT) is implemented on a hybrid machine tool LENS MTS 500 from Optomec. It consists of a directed energy deposition laser head for printing near-net shape components and a vertical rotating spindle to perform machining, grinding and polishing processes. This implementation allows the control of not just the geometric dimensions but also of the morphology (via grinding and polishing) and, to a limited extent, the material composition and microstructure by adjusting the laser heat-treatment parameters, all using the same datum in a machine tool. The single platform execution not only allows multiple process chains but also improves over conventional approaches in terms of enhancing forensics and traceability through the process chain, and thereby guaranteeing high levels of provenance.
Sensor fusion is essentially at the core of taking the data for action. The hybrid additive subtractive machine in is equipped with high-resolution acoustic emission, accelerometer and force sensors, as well as advanced imaging instruments. Additionally, researchers have developed a Dirichlet Process Gaussian State Machine model to represent dynamic intermittency, which is one of the most ubiquitous real-world transient behaviors.
The Institute for Manufacturing Systems has developed a fully unsupervised segmentation approach using a continuous max-flow formulation over the image domain while optimally estimating the flow parameters from the image characteristics. The flow capacities are then iteratively obtained by employing a novel Markov random field prior over the image domain. Comparative results with several state-of-the-art supervised as well as unsupervised methods suggest that the present method performs statistically similar to the supervised methods, but results in more than 90% improvement in the Dice score when compared to the state-of-the-art unsupervised methods.
Sponsors: Department of Energy/The Smart Manufacturing Institute, National Science Foundation
Autonomous Materials Synthesis and Discovery
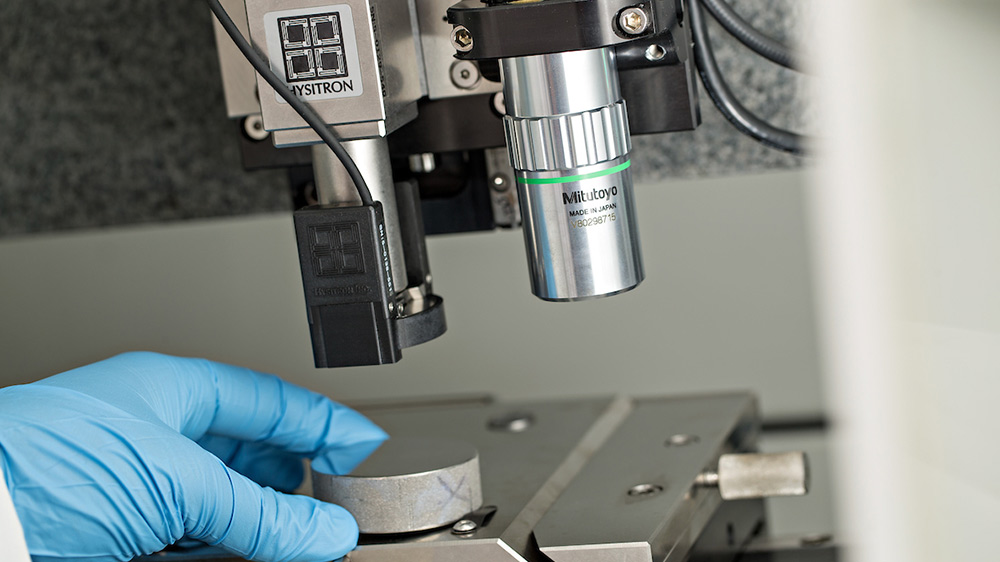
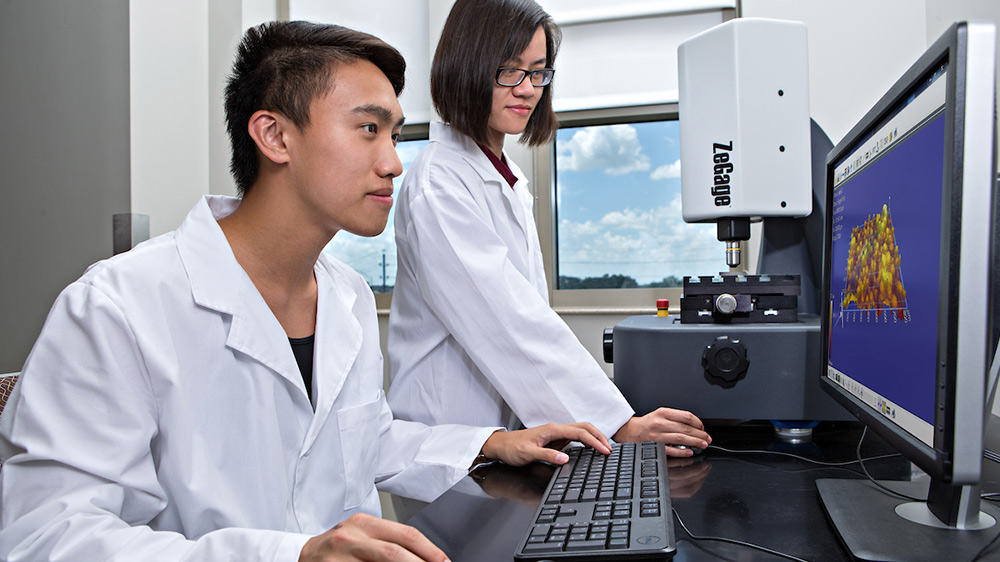
Recent hybrid additive-subtractive manufacturing platforms can usher a materials-on-demand manufacturing paradigm where the materials, along with geometry and surface morphology, are designed to meet the functionality. While in situ measurement systems have advanced to monitor geometric and morphological variations, microstructure and phase characterization methods remain slow, impeding this vision. To address this issue, researchers developed an approach to characterize the material concurrently during fabrication by associating in situ sensor measurements with the microstructures. Analysis of sensor data from machining of 316L steel suggests that the microstructural variations under different process parameters can be predicted in real time with 93% accuracy.
Sponsors: Texas A&M University X-Grants, National Science Foundation
Localized Magnetic Finishing of Freeform (Additive Manufacturing) Components
Researchers have developed and patented a novel magnetic concentration setup based on configuring a battery of electropermanent magnets capable of creating a localized spatiotemporal variation in the magnetic field near the workpiece surface. Using computational-mechanistic models as well as an experimental study, the Institute for Manufacturing Systems shows that the current configuration of electropermanent magnets is capable of amplifying the magnetic field strength by almost three times near the workpiece surface. Additionally, by modulating the strength and toggling the polarity of electropermanent magnets, it is possible to generate the required downforce and sloshing motion of the fluid at targeted locations without requiring any rotating part (unlike in most conventional magnetic polishing setups).
Sponsor: National Science Foundation
Cybersecurity for Manufacturing
The Institute for Manufacturing Systems systematically studied the cybersecurity risks in an emerging digital manufacturing context, assessed the impact on manufacturing and identified approaches to secure digital manufacturing. The emerging manufacturing technologies like additive/hybrid manufacturing enable small and medium enterprises to transform into cybermanufacturing kiosks that deliver manufacturing-as-a-service by digitizing much of the manufacturing workflow (design, communication and manufacturing). This transformation is causing a paradigm shift in which major producers and original equipment manufacturers can outsource manufacturing of components to distributed small and medium enterprises located near the point of need. The increasing reliance on a digital thread would reduce the burden of resiliency required from the physical supply chains. The Institute for Manufacturing Systems’ research has led to a novel design-sharing scheme for the digital thread based on video streaming to address the issue of intellectual property theft and tampering. The approach offers immense potential for the improvement of the cyber resilience of digital manufacturing supply chains.
Sponsor: SecureAmerica Institute